

Simplicity and accuracy are such two parameters. Simplicity Vs accuracy: – Engineering is all about trade off among different conflicting requirements. Usefulness of transfer function model is discussed latter. On the other hand for optimal control application state space model is useful.

For example, to find the transient or steady state response of SISO (Single Input Single Output) LTI (Linear Time Invariant) system transfer function model is useful. Use of the models depends on the application. From these input-output data we are to find the mathematical model of the system that it termed as system identification.ĭifferent mathematical models: – Commonly used mathematical models are. In this method the system is treated as a black box where we can only get the outputs due to different inputs used to excite the system. When we know the physical components of the system, we can apply the basic laws of physics to directly obtain a set of the differential equations as a mathematical model of the system. Methods of finding mathematical models: – One way of modeling a system is straight forward. SEE ALSO Introduction To Single-Board Microcontrollers
#Modeling differential equation systems software#
Although control engineering has sophisticated mathematical tools and software for system design, the above process of trial and error involving both of the synthesis and analysis is still inevitable to some extent. Hence according to the software simulation (analysis) we have to change the proposed model of the system such that it can be properly implanted. This is because, for the sake of computational ease we often neglect some of the practical aspects and the effect of the change in operating conditions as well as the parameter variations in the estimated model of the system. (In fact effect of noise and disturbances are also externally added to this analysis based on software simulation). This analysis shows that sometimes the system’s estimated model is unable to follow the desired output when the system is subjected to practical outputs. This task is analysis, as mentioned earlier. For this reason, the estimated model is simulated using different software to check whether the system is able to respond properly when it is excited by different inputs that the system is likely to face in real life. But this model can’t be directly realized using hardware without checking the fact how it behaves when it is subjected to different inputs. Undoubtedly this task is design or synthesis of the system that we have discussed earlier. Based on this information he has to estimate the mathematical model of the system. A control engineer first needs to know under different input or environmental conditions how the system behaves. we don’t know what is inside the box and in order to find what is inside it we excite the system by different test signals and measure or observe the nature of the response.ĭesign and analysis are closely related to each other as far as the construction of a control system is concerned. In such case the system is conceived as black box i.e.
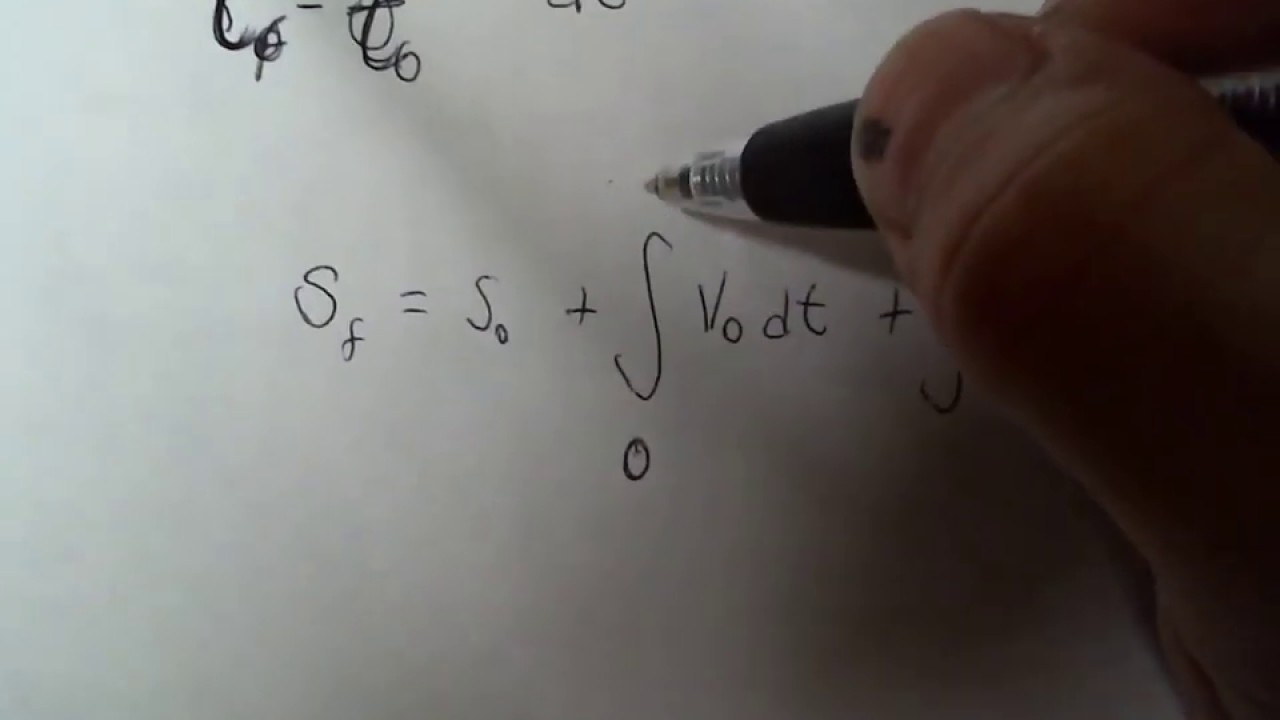
On the other hand, design or synthesis means we have to find out the system equations or the arrangement of the components, provided we know the output of the system for an input. Now one may inquire– what is meant by analysis and design? How modeling of control system is related to analysis and design?Īnalysis means the process of finding the response or output of a system when it is excited by an input or excitation provided we know the mathematical model of the system. It is nothing but the process or technique to express the system by a set of mathematical equations (algebraic or differential in nature). Mathematical modeling of any control system is the first and foremost task that a control engineer has to accomplish for design and analysis of any control engineering problem.
